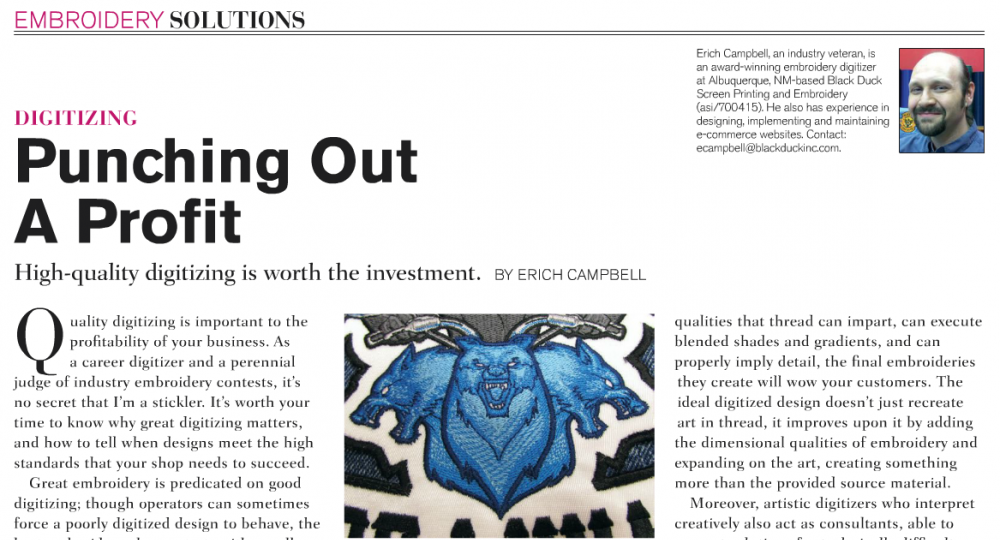
Quality embroidery digitizing is the backbone of great machine embroidery.
It’s not surprising that a career digitizer like myself would champion well-made files as one of the most important parts of any embroidery job- as an in-house digitizer, it’s not an advertisement of my services that makes be believe so highly in the role of the digitizer. My experience in production on the ground, brings me this holistic view of embroidery in which every step supports the next and for which good digitizing provides the foundation. January’s Wearables Magazine gave me the opportunity to provide some concrete reasons why I believe that high-quality embroidery digitizing is well worth the money spent. If you’d like the full detail, click here for the digital edition of the article; below is my summary of the key points.
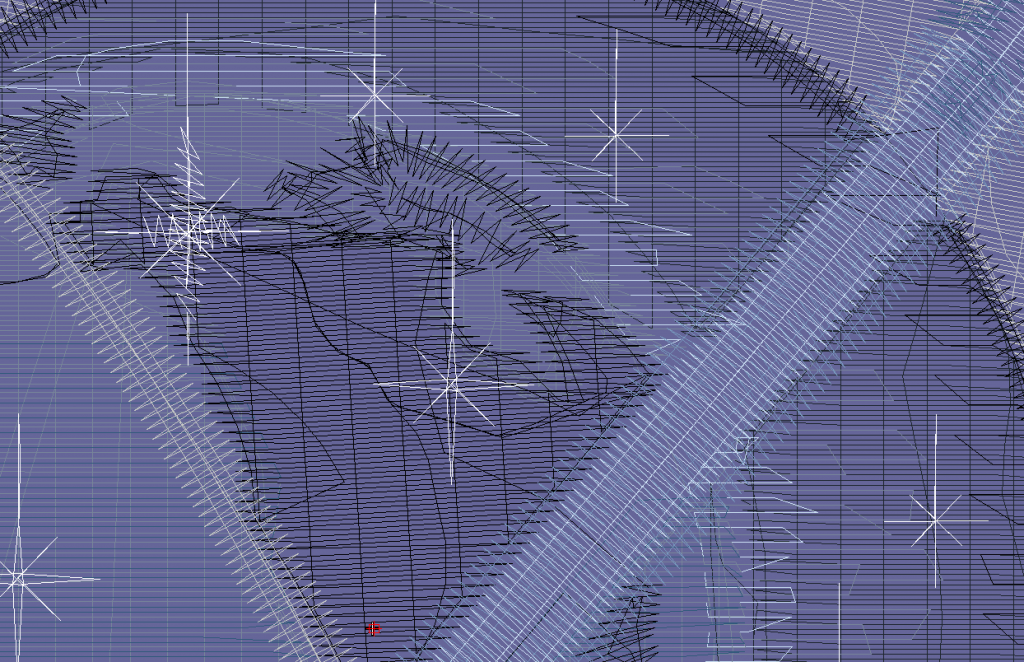
Detail of the digital file behind a blended patch that required considerable creativity in interpretation; no auto-conversion could take the details that needed alteration into account
Production Efficiency
Great digitizers use every stitch they need and none they don’t; a high quality file will run quicker, with little to no thread breakage and can even reduce the need for some support materials like extra stabilizers and toppings, depending on the execution. This is especially true as it relates to large-scale or long-term production, where excess color changes, trims, or thread breaks that might be forgivable in a small run balloon out to large losses with hundreds or thousands of runs.
Stitch Quality
Good digitizing eliminates some common flaws that cause customers to reject garments; combining the art provided with information about the garments; a good embroidery digitizer will return a file that creates the proper coverage without excess density, with proper registration of elements, and that doesn’t overly tax the garment to cause excess rippling, holes, or other problems with the garment’s hand.
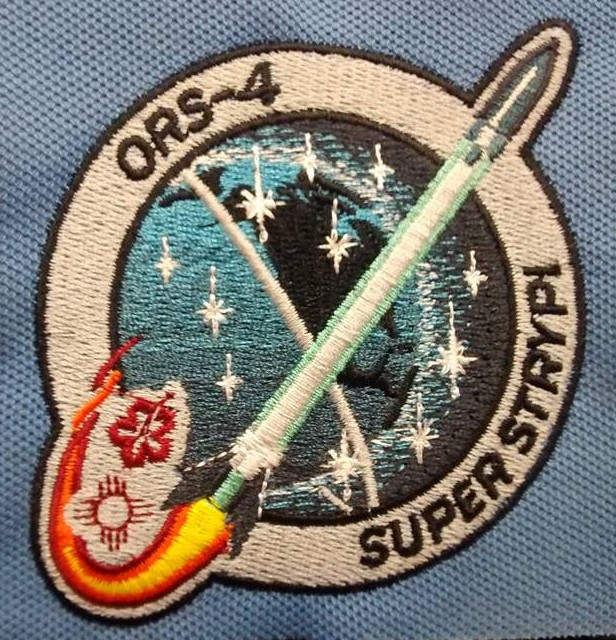
An initial sample run of the digitized file shown above- a great deal of detail had to be altered to arrive at this embroidery from the original, unfriendly art.
Artistic Interpretation
Though this is a subjective measure of digitizing, the best embroidery digitizers will use their knowledge of the medium to create the best interpretation of the provided art as an embroidery; this means that they will alter what must be altered in a respectful and artistic way, while suggesting proper alternatives when roadblocks occur with overly small or dense details. A truly great embroidery digitizer will use the unique, dimensional properties of thread to make an embroidered design something more than can be achieved in print alone, utilizing the thickness, sheen, and texture of the medium to create something unique and eye-catching.
It’s true that such digitizing may cost more initially, but efficient, clean, and thoughtfully created designs go a long way toward creating a stress-free production environment that keeps you effective and the quality execution that keeps customers coming back for more.
Do you have the full article? That link does not work.
Try this link- I will fix the one in the post. Thanks for letting me know! http://www.wearables-digital.com/publication/?i=348696&ver=html5&p=62